Here are 7 different types of gears that you might find inside a machine:
- Spur Gears
- Bevel Gears
- Straight Cut Gearing
- Worm Gear Drives
- Helical Gears
- Cylindrical Gears (straight teeth)
- Rack and Pinion
7 Different Types Of Gears
Spur Gears
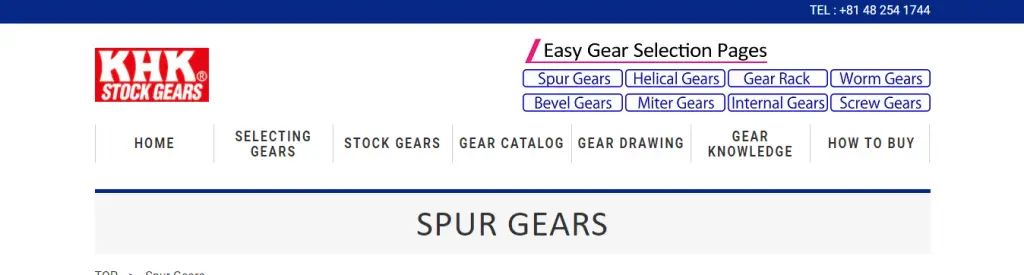
Spur gears are the most common type of gear. They have straight teeth, and they work well with other spur gears or back-and-forth movements. The advantage to using these types of gears is that they’re durable and simple in design – but not as strong as bevel Gears.
Features
- The Spur Gear is a type of gear that has teeth on the circumference, or “outside” edge
- A spur gear can be used in many different applications and industries, including automotive, aerospace, medical technology, and more
- Spur Gears are typically made from steel with an iron alloy to increase strength and durability
- Spur gears have a higher ratio than helical gears which means they carry larger loads at slower speeds
- Spur gears should not be lubricated since this will cause them to wear out faster
- There are three main types of spur gears – an external tooth (used for high-speed applications), an internal tooth (for low-cost applications), and hypoid tooth (a combination of external and internal)
Bevel Gears
These are also called “miter” gears because their two sets of teeth form a mitre angle (a diagonal). These can’t mesh together like regular spurs do without causing some backlash when you try to turn them at different speeds, so this limits their use for general applications unless it’s specifically designed for bevels. Bevels come into play more often in non-circular motion machines, such as jigsaws, lathes and grinding wheels.
Bevel gears are the best choice when working with other bevels because they can mesh together without any backlash. This makes them a great option for applications that need to transmit motion from one direction to another or in noncircular motions where there is some angular offset between the two axes of rotation. Bevel gears often last longer than spur gears due to their more complex design, which includes additional teeth designed specifically for transmitting torque (rotational force).
Features
- Bevel gears are a type of gear that is used for transmitting power in a straight line
- The teeth on the bevel gear can be either straight or spiral
- There are two types of bevel gears – external and internal
- Internal bevel gears are typically used when there is not enough space to install an external one
- External bevel gears have more strength than their internal counterparts, but they require more room for installation
- Bevel gears help reduce friction by operating at different speeds – this means less wear and tear on the machine as well as less noise being generated from the machinery
Straight Cut Gearing
A straight cut gear is a type of spur gear with teeth that are arranged in parallel to the shaft, and which have an equal number of male and female parts. Straight-cut gears can be thought of as an assembly of matched pairs (or couples) on meshing centers. They transfer power from one rotating shaft to another through their teeth when they rotate together at speeds for which the ratio between them matches the speed ratio being transmitted.
The tooth profiles are flat or straight across most (but not all) surfaces; this basic shape was used by humans over two thousand years ago for saw blades, chisels and axes because it wears well due to its large contact area relative to its thickness.
Features
- Straight-cut gearing is a type of gear system that produces less noise and vibration
- In straight-cut gearing, the teeth are shaped in a straight line (hence the name)
- The gears are usually mounted on one or more shafts, which can be parallel to each other or at an angle to each other
- The teeth have no helical shape; instead, they form a flat surface with tooth thicknesses that vary gradually from one side of the tooth to the other
- Straight-cut gears are typically used for high-precision applications such as machine tools and clocks because their accuracy permits them to mesh together without backlash under heavy loads
- A disadvantage of this design is that it has only two contact points between mating gears, which means there’s less metal-to-metal contact area than in traditional spur gears
Worm Gear Drives
Worm gear drives are usually used for high precision, low-speed applications. Those uses include machine tools and clocks. One of the advantages is that there’s less metal-to-metal contact area than in traditional spur gears. However, they’re more expensive to produce and can’t be built on a large scale like other types of gears.
The teeth have no helical shape; instead, they form a flat surface with tooth thicknesses that vary gradually from one side of the tooth to the other – think about how worms spin when their bodies move around a central axis or axle because these gears work just like them! In order to make worm drive systems efficient, engineers must design their products as close as possible to perfect balance.
Features
- Worm gears are a type of gear that is used in applications where large amounts of power must be transmitted with relatively little mechanical effort
- The worm and wheel contact surfaces are non-circular to ensure constant meshing, even under heavy loads
- This design is ideal for use in moving objects such as cranes, elevators, and conveyors because it can transmit significant torque while rotating at low speeds
- In addition to this, the teeth on worm gears always maintain constant contact with each other when they are turned – which means less wear over time
- This makes them perfect for high-stress or high-load applications
Helical Gears
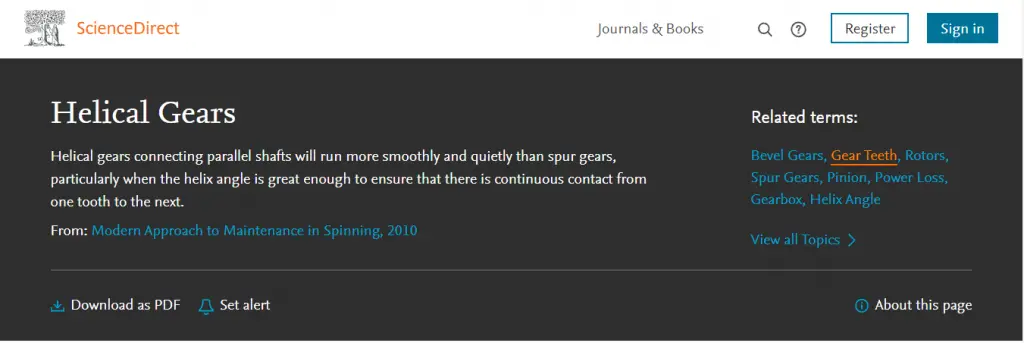
Helical gears are circular gear with teeth cut in it. These types of gears interlock and can be used to transmit torque smoothly from one shaft to another at a constant speed. This design is often chosen for its durability and ability to resist shock loads as the bearings do not slide on the axle when they turn – instead, they roll along their surfaces. In addition, helix-shaped gearing will maintain contact between the two parts being turned throughout their rotation; this means that there is less axial load exerted by these components because they never lose contact with each other during operation.
Features
- Helical gears are a type of bevel gear
- They can be used in various applications, including aerospace and manufacturing
- The teeth on helical gears have an angle that is steeper than spur or straight-cut gears
- They’re also quieter because they don’t make contact with each other like other types of gears do
- Helical gearing is beneficial for any application where noise reduction and efficiency are important
- One example would be the automotive industry – it’s been estimated that using helical gearing could reduce engine noise by up to 30%!
Cylindrical Gears
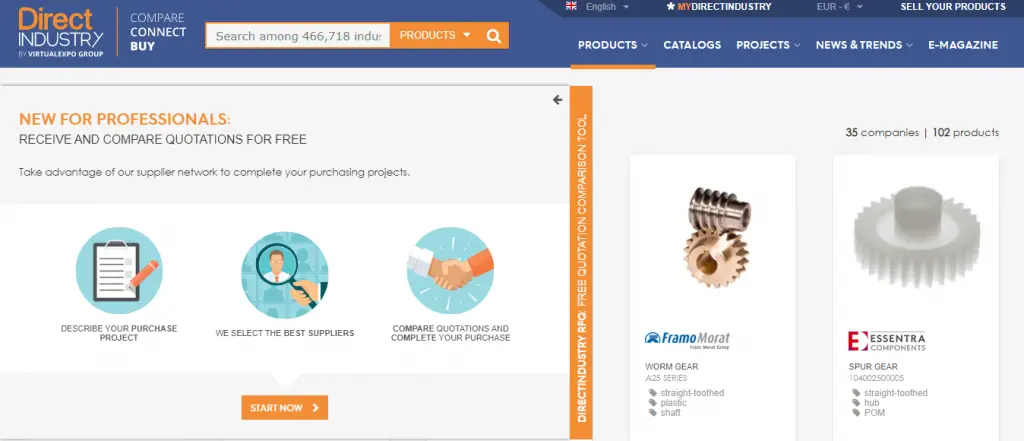
Cylindrical gears are used when the input shaft is mounted horizontally and the output shaft vertically.
These types of gears provide a continuous transmission of power from input to output, which features an even load distribution throughout the operation. They’re also one type of gear where teeth are right-handed (clockwise) on both sides – this can create smoother motion because there’s no need for shifting as with other types of gearing.
The tooth design on cylindrical gives them three contact points at any given time during their rotation, making it easier to operate in a higher speed range without damaging themselves or mating components like worm wheels and screws do
Additionally, many industrial applications require heavy axial loads that would quickly destroy straight-cut or spur gears.
Features
- Cylindrical gears are used in many different industries to provide a more efficient way of turning an object
- They can be found on factory equipment, such as conveyor belts and machine tools
- These types of gears have a lot of advantages over other types of gears because they offer less friction, allow for smoother operation, and work better at high speeds
- The major disadvantage is that these cylinders cannot handle heavy loads or forces applied perpendicularly to the axis
- One way to increase their strength is by using steel backing plates which also helps with load-handling capabilities
- Steel backing plates can also help reduce noise levels within machinery where cylindrical gears are present
Rack And Pinion
The rack and pinion is a type of gear that has teeth on the same surface. The toothless side is shaped in a way similar to an egg beater, with two cones joined by parallel rods at their base called “spurs”.
This design allows one cone to rotate while the other remains stationary. This style of gear consists mostly of brass or steel pins (which are rigid members) mounted closely together such as organ pipes, which turn when driven by pressure from the air blown across them like bird feathers; these types of gears have no more than 30 teeth and can handle only light loads because they cannot reverse direction quickly enough due to their lack of engagement surfaces between mating parts
Rack and Pinions allow for smooth operation along a straight axis of rotation. They consist of gear with teeth on one surface and a thin, pin-shaped shaft that meshes with it. The rod is usually mounted perpendicular to the plane in which the driven member operates.
Features
- Rack and pinion is a type of steering mechanism
- It’s an improvement over the older style “worm gear” system
- The rack and pinion system uses a series of gears to turn the wheels in response to turning the steering wheel
- This design makes it easier for drivers to control their vehicles
- When used on cars, this design can be found in both front-wheel drive and rear-wheel drive configurations
- In contrast, most modern cars use power-assisted rack and pinion systems that provide better handling when driving at low speeds or around corners
References:
https://www.iqsdirectory.com/articles/gear/types-of-gears.html
https://www.rexnord.com/blog/articles/gear/types-of-gears